На кафедре систем пластического деформирования МГТУ «СТАНКИН» разработаны несколько технологических процессов объемной штамповки деталей сложной формы, реализацию которых с большим экономическим эффектом следует вести с использованием прессов двойного и тройного действия. Предлагаемые новые технологические процессы охватывают большую группу деталей типа: воротниковых и др. фланцев для арматуростроения (нефтегазовая промышленность), пробок шаровых, корпусов задвижек, корпусов водо" и теплосчетчиков из латуни взамен чугунного литья и других деталей сложной формы.
Известные технологические процессы штамповки воротниковых фланцев (ГОСТ 12821) и фланцев со втулкой для нефтегазовой промышленности, в зависимости от серийности их производства, отличаются большим разнообразием и, в ряде случаев, их следует отнести к затратным технологиям. Так, например, фланцы с развитой втулочной частью и фланцевые переходы зачастую (фирма «АТЭК» и др.) изготавливают методом сварки плоского фланца (получаемого газоплазменной вырезкой из толстолистовой заготовки) со втулкой из трубной заготовки.
Для массового производства воротниковых фланцев Воронежский завод ЗАО «ТЯЖМЕХПРЕСС» создал несколько линий горячей облойной штамповки воротниковых фланцев с максимальным диаметром до 700 мм (фланцы Ду 18", с использованием КГШП силой 125 МН) [1]. С целью значительного снижения технологических сил штамповки фланцев и уменьшения расхода металла нами предлагается новый технологический процесс безоблойной штамповки из кольцевого полуфабриката. Исходная заготовка в виде кольцевого полуфабриката в зависимости от серийности производства может быть получена методом горячего выдавливания [2], методом гибки и сварки либо отрезкой от толстостенной трубы [3, 4].
В патенте «Станкина» (МКП 7В21/00, заявка 2003109601/02(010217) от 04.04.2003 «Способ горячей штамповки фланца со втулкой») предлагается перспективный технологический процесс штамповки фланцев из стали и цветных металлов и сплавов, позволяющий вести штамповку крупногабаритных фланцев диаметром до 1000 мм и более.
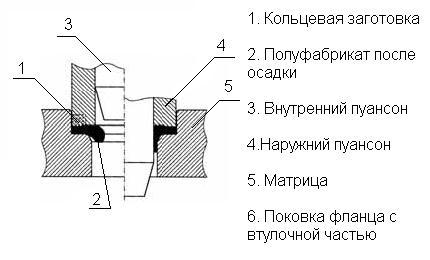
Фланец формируется из кольцевого полуфабриката (1) осадкой наружным пуансоном (4) с последующим формообразованием втулочной части поковки сдвиговой деформацией полуфабриката (2) внутренним конусным пуансоном (3). Внутренний пуансон осуществляет операцию протяжки. Таким образом, за один рабочий цикл пресса двойного действия формируется фланец со втулочной частью, что позволяет повысить производительность и снизить металлоемкость за счет ликвидации операции сварки плоского или воротникового фланца с переходом (втулкой).
Технологическая сила, затрачиваемая на реализацию процесса осадки (Рос) по предлагаемому методу, для фланца Ду 300 с наружным диаметром 510 мм равна 12 МН, а сила протяжки Р составляет 7 МН. При штамповке аналогичного фланца методом прямого горячего выдавливания из кольцевой заготовки [3] по требовался бы КГШП силой 40 МН.
Практически для реализации этого нового технологического процесса в отечественном машиностроении имеются только два гидравлических пресса: для крупных
фланцев (диаметром до 1000 мм) пресс двойного действия силой 120/80 МН, штампующий поковки типа полусфери др., на Белгородском арматурном заводе и для средних фланцев (диаметром до 500 мм) пресс тройного действия силой 20/10/10 МН, установленный в 2002 г. на ОАО «Автоспецмаш» (г. Череповец) [6]. Пресс обладает большими технологическими возможностями, и его конструкция может быть использована как один из вариантов при создании гаммы прессов двойного действия силой от 5/5 до 125/80 МН. Отличительной особенностью пресса конструкции ОАО «Автоспецмаш» является отказ от применения для привода ползуна гидроцилиндров прямого действия и замене их на ползунно"коленный привод. Как известно, такой привод обеспечивает значительное увеличение усилия к концу хода ползуна в нижней мертвой точке. В этом прессе два главных рабочих гидроцилиндра, размещенные снаружи станины, в сочетании с двумя двуплечими коромыслами и двумя шатунами образуют ползунно-коленный привод основного ползуна, развивающего силу до 25 МН. На ползуне смонтирован узел привода верхнего внутреннего пуансона-прошивня с силой до 10 МН и верхнего выталкивателя в виде гидроцилиндров с независимой системой управления. Под столом на станине пресса в приямке смонтирован узел привода нижнего пуансона-прошивня с силой до 10 МН и нижнего выталкивателя также в виде гидроцилиндров с независимой системой управления. Принципиальная схема размещения рабочих частей силовых органов пресса тройного действия применительно к разработанной нами технологии безоблойной штамповки пробки шаровой на Ду 100, 150 и 200 представлена на Рис. 2.
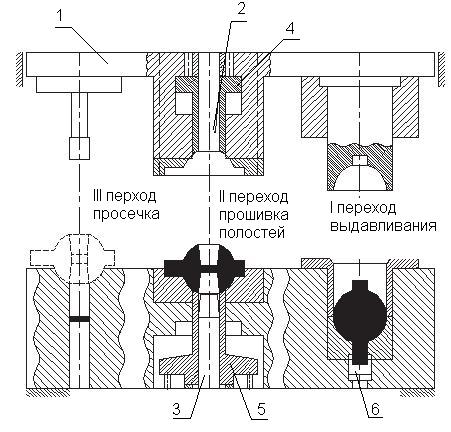
Рис.2. Схема размещения рабочих частей силовых органов горячештамповочного пресса тройного
действия и переходы штамповки пробки шаровой
Гидромеханическая система ползунно-коленного привода ползуна обеспечивает работу пресса с объемным расходом 23,5 л/сек, что позволило значительно сократить габариты гидропривода. Схема гидропривода пресса позволяет регулировать рабочее давление в гидросистеме, что обеспечивает работу пресса в разных силовых режимах в зависимости от изготавливаемой номенклатуры поковок. Пресс имеет массу вместе с гидроприводом 74 т, а его высота 5,3 м. Он установлен в агрегате с печью газового нагрева и раскатной машиной. Раскатка колец до 1000 мм осуществляется непосредственно после штамповки кольцевого полуфабриката, т.е. за один нагрев заготовки. На прессе была отработана технология горячей штамповки (t=750 0C) корпуса водосчетчика Ду 40 из латуни ЛС59-1 для ОАО «Завод Водоприбор». Штампов ка велась из прутка диаметром 80 мм с использованием сил на наружном ползуне ~ 5 МН и столько же на внутреннем пуансоне"прошивне. Масса поковки 2,9 кг. Габариты по длине — 190 мм. Нами совместно с ВНИИМЕТМАШ отработана технология комбинированного выдавливания фланца диаметром 190 мм (Рис. 5) с развитой втулочной частью на гидравлическом прессе двойного действия [7]. Максимальная сила, развиваемая центральным пуансоном, была равна 2500 КН. Фланец получали поперечным выдавливанием за первый ход центрального ползуна, а втулочную часть — обратным выдавливанием за второй ход.Аналогичная технология штамповки из сортового проката была успешно опробована на прессе «Автоспецмаш». При этом наружный диаметр фланца равен 260 мм, а внутренний диаметр втулки — 120 мм.Удельные силы выдавливания фланца и втулки из стали 20 находились в пределах 320"350 МПа (t=1150 0С).
Известные технологические процессы штамповки воротниковых фланцев (ГОСТ 12821) и фланцев со втулкой для нефтегазовой промышленности, в зависимости от серийности их производства, отличаются большим разнообразием и, в ряде случаев, их следует отнести к затратным технологиям. Так, например, фланцы с развитой втулочной частью и фланцевые переходы зачастую (фирма «АТЭК» и др.) изготавливают методом сварки плоского фланца (получаемого газоплазменной вырезкой из толстолистовой заготовки) со втулкой из трубной заготовки.
Для массового производства воротниковых фланцев Воронежский завод ЗАО «ТЯЖМЕХПРЕСС» создал несколько линий горячей облойной штамповки воротниковых фланцев с максимальным диаметром до 700 мм (фланцы Ду 18", с использованием КГШП силой 125 МН) [1]. С целью значительного снижения технологических сил штамповки фланцев и уменьшения расхода металла нами предлагается новый технологический процесс безоблойной штамповки из кольцевого полуфабриката. Исходная заготовка в виде кольцевого полуфабриката в зависимости от серийности производства может быть получена методом горячего выдавливания [2], методом гибки и сварки либо отрезкой от толстостенной трубы [3, 4].
В патенте «Станкина» (МКП 7В21/00, заявка 2003109601/02(010217) от 04.04.2003 «Способ горячей штамповки фланца со втулкой») предлагается перспективный технологический процесс штамповки фланцев из стали и цветных металлов и сплавов, позволяющий вести штамповку крупногабаритных фланцев диаметром до 1000 мм и более.
Рис.1. Схема изготовления поковки фланцевого перехода
на гидравлическом прессе двойного действия.
на гидравлическом прессе двойного действия.
Фланец формируется из кольцевого полуфабриката (1) осадкой наружным пуансоном (4) с последующим формообразованием втулочной части поковки сдвиговой деформацией полуфабриката (2) внутренним конусным пуансоном (3). Внутренний пуансон осуществляет операцию протяжки. Таким образом, за один рабочий цикл пресса двойного действия формируется фланец со втулочной частью, что позволяет повысить производительность и снизить металлоемкость за счет ликвидации операции сварки плоского или воротникового фланца с переходом (втулкой).
Технологическая сила, затрачиваемая на реализацию процесса осадки (Рос) по предлагаемому методу, для фланца Ду 300 с наружным диаметром 510 мм равна 12 МН, а сила протяжки Р составляет 7 МН. При штамповке аналогичного фланца методом прямого горячего выдавливания из кольцевой заготовки [3] по требовался бы КГШП силой 40 МН.
Практически для реализации этого нового технологического процесса в отечественном машиностроении имеются только два гидравлических пресса: для крупных
фланцев (диаметром до 1000 мм) пресс двойного действия силой 120/80 МН, штампующий поковки типа полусфери др., на Белгородском арматурном заводе и для средних фланцев (диаметром до 500 мм) пресс тройного действия силой 20/10/10 МН, установленный в 2002 г. на ОАО «Автоспецмаш» (г. Череповец) [6]. Пресс обладает большими технологическими возможностями, и его конструкция может быть использована как один из вариантов при создании гаммы прессов двойного действия силой от 5/5 до 125/80 МН. Отличительной особенностью пресса конструкции ОАО «Автоспецмаш» является отказ от применения для привода ползуна гидроцилиндров прямого действия и замене их на ползунно"коленный привод. Как известно, такой привод обеспечивает значительное увеличение усилия к концу хода ползуна в нижней мертвой точке. В этом прессе два главных рабочих гидроцилиндра, размещенные снаружи станины, в сочетании с двумя двуплечими коромыслами и двумя шатунами образуют ползунно-коленный привод основного ползуна, развивающего силу до 25 МН. На ползуне смонтирован узел привода верхнего внутреннего пуансона-прошивня с силой до 10 МН и верхнего выталкивателя в виде гидроцилиндров с независимой системой управления. Под столом на станине пресса в приямке смонтирован узел привода нижнего пуансона-прошивня с силой до 10 МН и нижнего выталкивателя также в виде гидроцилиндров с независимой системой управления. Принципиальная схема размещения рабочих частей силовых органов пресса тройного действия применительно к разработанной нами технологии безоблойной штамповки пробки шаровой на Ду 100, 150 и 200 представлена на Рис. 2.
Рис.2. Схема размещения рабочих частей силовых органов горячештамповочного пресса тройного
действия и переходы штамповки пробки шаровой
Гидромеханическая система ползунно-коленного привода ползуна обеспечивает работу пресса с объемным расходом 23,5 л/сек, что позволило значительно сократить габариты гидропривода. Схема гидропривода пресса позволяет регулировать рабочее давление в гидросистеме, что обеспечивает работу пресса в разных силовых режимах в зависимости от изготавливаемой номенклатуры поковок. Пресс имеет массу вместе с гидроприводом 74 т, а его высота 5,3 м. Он установлен в агрегате с печью газового нагрева и раскатной машиной. Раскатка колец до 1000 мм осуществляется непосредственно после штамповки кольцевого полуфабриката, т.е. за один нагрев заготовки. На прессе была отработана технология горячей штамповки (t=750 0C) корпуса водосчетчика Ду 40 из латуни ЛС59-1 для ОАО «Завод Водоприбор». Штампов ка велась из прутка диаметром 80 мм с использованием сил на наружном ползуне ~ 5 МН и столько же на внутреннем пуансоне"прошивне. Масса поковки 2,9 кг. Габариты по длине — 190 мм. Нами совместно с ВНИИМЕТМАШ отработана технология комбинированного выдавливания фланца диаметром 190 мм (Рис. 5) с развитой втулочной частью на гидравлическом прессе двойного действия [7]. Максимальная сила, развиваемая центральным пуансоном, была равна 2500 КН. Фланец получали поперечным выдавливанием за первый ход центрального ползуна, а втулочную часть — обратным выдавливанием за второй ход.Аналогичная технология штамповки из сортового проката была успешно опробована на прессе «Автоспецмаш». При этом наружный диаметр фланца равен 260 мм, а внутренний диаметр втулки — 120 мм.Удельные силы выдавливания фланца и втулки из стали 20 находились в пределах 320"350 МПа (t=1150 0С).